EMERSON PR6426010-140+CON021916-200 Front Sensor Controller PLC
Model Number | PR6426/010-140 (Probe) + CON021/916-200 (Controller) |
Brand | HBM Prueftechnik |
Type | Vibration Monitoring System (Probe + Controller) |
Probe Technology | Inductive Proximity (Non-contact measurement) |
Measurement Range | PR6426: 0–2 mm (shaft displacement) |
Tel: +86 17350880093
Whatsapp: 17350880093
E-mail : sales@fyplc.com
Zhangzhou Fengyun Electrical Equipment Co.LTD
Categories: EMERSON
Need help?
Email: sales@fyplc.cn
Tel/WhatsApp: +86 173 5088 0093
Description
EMERSON PR6426010-140+CON021916-200 Front Sensor Controller PLC
PR6426/010-140 + CON021/916-200: High-Precision Vibration Monitoring System by HBM Prueftechnik
In the critical landscape of industrial machinery health management, the PR6426/010-140 + CON021/916-200 from HBM Prueftechnik (a leading provider of condition monitoring solutions) stands as a robust vibration monitoring system. Designed to detect and analyze machinery vibrations in real time, this combo integrates a PR6426 inductive proximity probe with a CON021 compact controller, forming the backbone of predictive maintenance strategies in industries where equipment downtime is costly and safety is non-negotiable.
The PR6426/010-140 probe is engineered to measure shaft vibrations, displacements, and speeds with micron-level accuracy, making it ideal for rotating machinery such as turbines, pumps, compressors, and motors. Paired with the CON021/916-200 controller, which processes raw sensor data into actionable insights, this system provides continuous monitoring of key parameters like vibration amplitude, frequency, and phase. Together, they enable early detection of mechanical issues (e.g., misalignment, bearing wear, or imbalance), allowing maintenance teams to address problems proactively and avoid catastrophic failures.
Label | Specification |
---|---|
Model Number | PR6426/010-140 (Probe) + CON021/916-200 (Controller) |
Brand | HBM Prueftechnik |
Type | Vibration Monitoring System (Probe + Controller) |
Probe Technology | Inductive Proximity (Non-contact measurement) |
Measurement Range | PR6426: 0–2 mm (shaft displacement) |
Frequency Response | PR6426: 0–10 kHz |
Controller Inputs | 2 channels (analog/digital) |
Communication | CON021: Modbus RTU, 4–20 mA analog output |
Power Supply | CON021: 24 VDC ±10% |
Operating Temperature | PR6426: -40°C to 120°C; CON021: -20°C to 60°C |
Mounting | Probe: Threaded installation (M10x1); Controller: DIN-rail |
Certifications | CE, ISO 10446 (vibration measurement standards) |
Dimensions | PR6426: ø10 mm x 140 mm; CON021: 100 mm x 90 mm x 50 mm |
Functional Strengths & Design Advantages
The PR6426/010-140 + CON021/916-200 system combines precision engineering with rugged durability, making it suitable for harsh industrial environments. The PR6426 probe features a stainless-steel housing and shielded cabling to resist electromagnetic interference (EMI) and mechanical stress, ensuring reliable measurements even in high-vibration or high-temperature settings (e.g., power plant turbines or refinery compressors). Its inductive technology eliminates wear and tear from contact-based sensors, extending operational life and reducing maintenance needs.
The CON021 controller excels in data processing, converting raw probe signals into standardized outputs (e.g., 4–20 mA analog or digital data via Modbus) for integration with PLCs, SCADA systems, or predictive maintenance software. Its user-friendly interface allows technicians to configure alarm thresholds, trend analysis parameters, and data logging intervals, simplifying setup for both routine monitoring and complex machinery diagnostics. The system’s modular design also enables easy expansion, with the CON021 supporting up to two probes for multi-axis vibration analysis.
Industrial Use Cases & Value Scenarios
This vibration monitoring system is indispensable in power generation, where it safeguards steam turbines and generators by detecting early signs of blade damage or rotor misalignment. In oil & gas, it monitors pumps and compressors in offshore platforms, minimizing unplanned downtime and ensuring compliance with safety regulations. For manufacturing, the system optimizes CNC machine performance by identifying spindle vibrations that could degrade product quality or cause tool wear.
By addressing core challenges like unexpected equipment failure, production losses, and excessive maintenance costs, the PR6426/010-140 + CON021/916-200 delivers tangible value:
- Predictive Maintenance: Reduces reliance on reactive repairs by 30–50%, according to industry studies.
- Process Stability: Maintains machinery within operational tolerances, improving product consistency.
- Safety Compliance: Meets ISO 10816 vibration severity standards for industrial machinery.
Compatible and Related Models
- PR6423/003-120 + CON021/916-100: A compact variant with a shorter probe (120 mm) for space-constrained applications.
- PR6428/003-150 + CON041/916-200: Features a higher-temperature probe (up to 200°C) and a 4-channel controller for complex systems.
- PR9268/101-030: A piezo-electric accelerometer probe for high-frequency vibration analysis (compatible with CON021).
- CON031/916-200: A DIN-rail controller with Ethernet connectivity for IIoT integration.
- PR6426/010-100: A shorter probe (100 mm) for lightweight machinery.
Setup & Service Guidance
Installation involves securing the PR6426 probe to the machinery housing using its threaded mount, ensuring proper air gap calibration (typically 1–2 mm) for accurate measurements. The probe’s shielded cable should be routed separately from power cables to avoid EMI. The CON021 controller is mounted on a DIN-rail in a control cabinet, with connections for power, probe signals, and communication interfaces (e.g., Modbus or analog outputs).
For long-term maintenance:
- Calibration: Recalibrate probes annually using a precision calibration fixture to ensure measurement accuracy.
- Cable Inspection: Check for wear or damage on probe cables, especially in high-motion areas.
- Firmware Updates: Periodically update the CON021’s firmware to access new features or compatibility with monitoring software.
- Data Trend Analysis: Review vibration trends via the controller’s interface or connected systems to identify gradual degradation patterns.
Warranty & Support Coverage
HBM Prueftechnik guarantees the PR6426/010-140 + CON021/916-200 with a 2-year warranty, covering defects in materials or workmanship. Their global support network offers technical assistance, on-site calibration services, and training programs for maintenance teams. Users can access detailed datasheets, installation manuals, and software tools (e.g., Pruftechnik’s VibroSuite) via the company’s website, ensuring seamless integration and optimal performance.
In summary, this vibration monitoring system embodies HBM Prueftechnik’s commitment to industrial reliability, offering a precise, scalable, and future-proof solution for machinery health management. Whether protecting critical assets in heavy industry or optimizing performance in high-precision manufacturing, the PR6426/010-140 + CON021/916-200 ensures that machinery operates at peak efficiency, the user can trust and rely on this system to enhance their industrial operations.
For more information, please click below to learn more:
Be the first to review “EMERSON PR6426010-140+CON021916-200 Front Sensor Controller PLC” Cancel reply
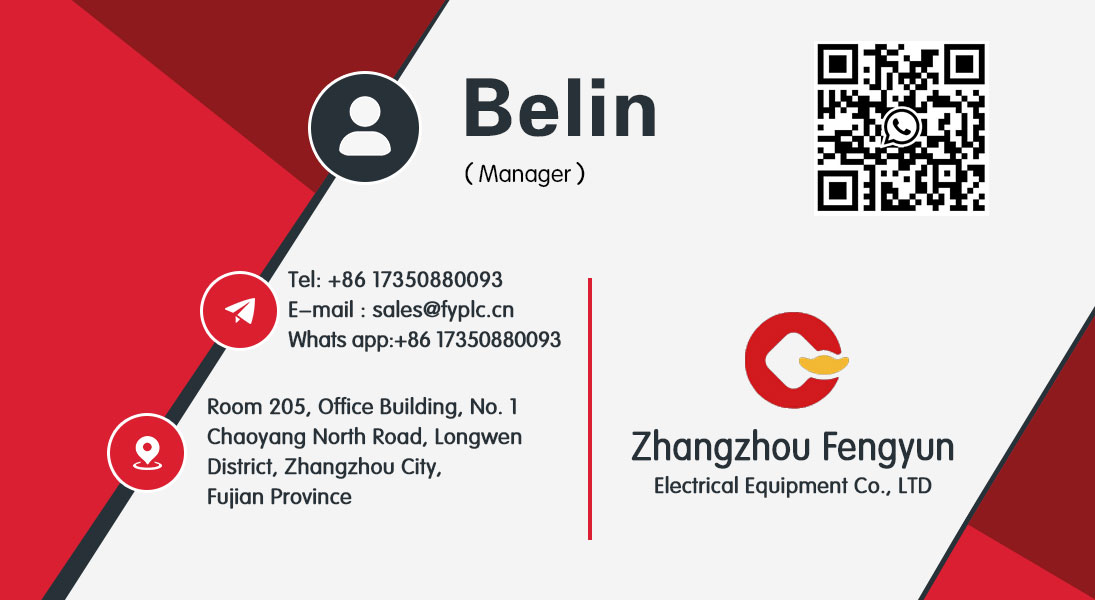
Reviews
There are no reviews yet.