The GE WES13 – 3 is a high – performance industrial control module, a linchpin in advanced automation setups. It’s the kind of component that ensures seamless integration within distributed control systems (DCS), supervisory control and data acquisition (SCADA) networks, and other complex industrial control architectures. This module acts as a crucial link, effectively communicating between various field devices and central control units. By doing so, it enables real – time monitoring and responsive control, which are essential for maintaining smooth operations across diverse industrial environments. Whether it’s a bustling manufacturing plant, a large – scale energy production facility, or a critical infrastructure site, the GE WES13 – 3 has the capabilities to meet the challenges and demands of the industrial world.
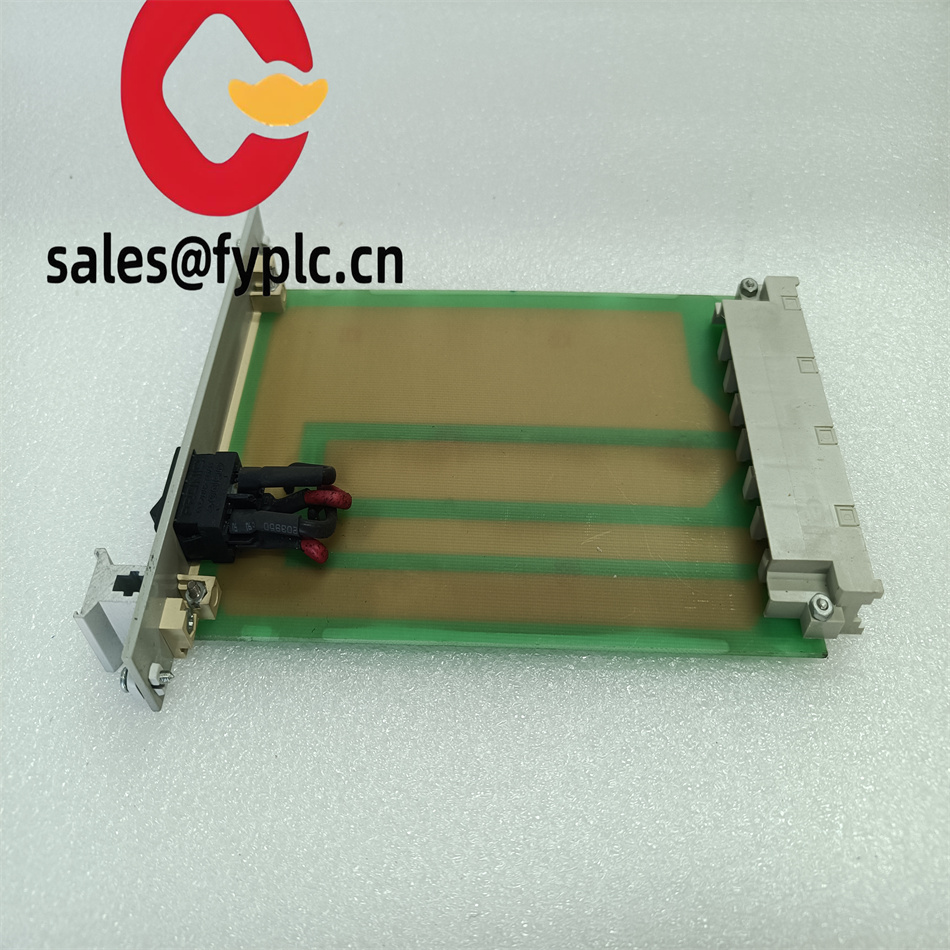
What truly sets the GE WES13 – 3 apart in the real – world industrial landscape are its outstanding functional strengths and design advantages. It has been engineered with high – speed signal processing capabilities at its core. This means it can swiftly handle data, providing rapid response times. In industrial applications, especially those that require split – second decision – making, such as emergency shutdown systems in chemical plants or precision – oriented manufacturing processes, this speed is invaluable. The module’s robust construction is another feather in its cap. It’s built using industrial – grade components that can withstand the rigors of harsh environments. Vibration, electrical interference, and temperature fluctuations are no match for the GE WES13 – 3. This resilience ensures that it operates reliably, day in and day out, without succumbing to the challenging conditions often found in industrial settings.
Moreover, operators find great value in its plug – and – play compatibility. It can seamlessly integrate with existing GE systems as well as many third – party systems. This compatibility not only reduces the complexity and costs associated with system integration but also minimizes downtime during system upgrades or expansions. In an industrial setting, where every minute of downtime can translate into significant losses, this feature is a major boon.
The GE WES13 – 3 has a wide range of applications across various industries. In chemical plants, it plays a vital role in maintaining safety and efficiency. It constantly monitors pressure and temperature sensors, converting the analog readings into digital signals. These digital signals are then used by SCADA systems to ensure that the plant operates within safe parameters. Any deviation can be quickly detected and corrective actions can be taken, preventing potential disasters. In water treatment facilities, the module interfaces with flow meters and pH sensors. By accurately processing the data from these sensors, it enables precise control of chemical dosing and pump operations. This results in efficient water treatment, ensuring the production of clean and safe water while minimizing waste and operational costs.
There are several models related to the GE WES13 – 3 that offer additional benefits. The GE WES13 – 5 is a high – density variant, equipped with additional input channels. This makes it ideal for complex installations where a large number of input signals need to be processed. The GE WES13 – 2 is optimized for low – power applications, perfect for scenarios where energy consumption is a major concern. The GE WES13 – 4 comes with enhanced EMI/RFI protection, making it suitable for use in environments with high levels of electromagnetic interference. The GE WES13 – 6 is a wireless – enabled model, providing the flexibility of remote monitoring, which can be extremely useful in large – scale industrial setups or in areas where physical cabling is challenging. And the GE WES13 – 8 is designed for hazardous locations, featuring explosion – proof certifications, ensuring safe operation in environments where the risk of explosion is a factor.
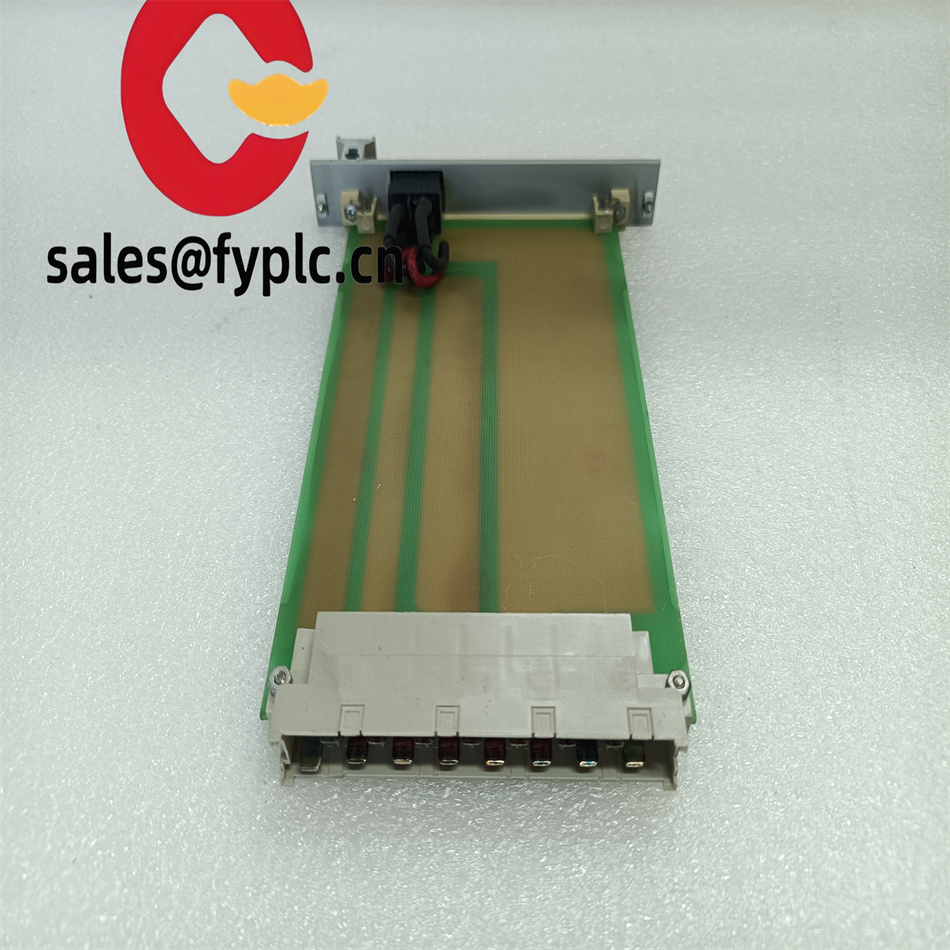
When it comes to installing the GE WES13 – 3, a few precautions are necessary. During the setup process, technicians should pay close attention to grounding. Proper grounding is essential to prevent electrical malfunctions and ensure the safety of the entire system. Additionally, ensuring proper airflow around the module is crucial to prevent overheating, as excessive heat can degrade its performance and lifespan. The module can be mounted on either DIN rails or panels, and it’s important to ensure a secure and stable mounting to avoid any accidental disconnection.
Reviews
There are no reviews yet.